(1) Increase the gate's size or increase the number of gates.
(2) Change the gate's position.
(3) Reduce the injection speed, multi-stage injection can be used and only reduce
the speed when the molten resin goes through the gate.
(4) Reducing the viscosity of resin; increase resin temperature, mold temperature, etc.
(5) Check the pressure maintaining.
(6) Increase the temperature of the barrel.
(7) A circular arc transition should be provided between the gate and the mold wall.
4.
The example analysis of jetting
In the production of a back cover of a mobile phone, the customer specified the gate location, and at the same time restricted its structure and gate location not to be changed, as shown in Figure 3. After the trial production, it was found that the product had a serious jetting and insufficient filling, as shown in Figure 4. First, the method of adjusting the molding process parameters was adopted, but it was found that there were still defects in the parts. The adjustment of the molding process parameters failed. Meanwhile, because of the appearance requirements for the mobile phone's case, generally, only point gates can be used. The jetting cannot be eliminated by increasing the gate's size. Therefore, we try to reduce the viscosity of the resin to improve the jetting and analyze the filling state of different plastic materials by using Moldflow.
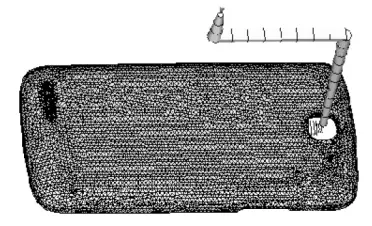
Figure 3 Locations of gates
Figure 4 Jetting
According to the strength requirement for the part, the first selected material is PC (polycarbonate) in the design. Use Moldflow to analyze the filling of the part; check whether the filling process of the part is balanced and whether the part can be completely filled. The filling pressure is 139.75 MPa and the flow rate is 20.02cm3/s. Figure 5 shows the results of the filling analysis of
PC. It can be seen that the temperature of the front melt flow reaches 322℃ from Figure 5, and there is a lack of materials and cold shuts at the end of the product.
Figure 5 Analysis results of PC filling
Given a lack of materials in the selection of PC, PC plus ABS are now selected. The viscosity of PC plus ABS is lower than that of PC, and its filling pressure is 120.31MPa; the flow rate is 15.37cm3/s. Figure 6 shows the filling analysis of PC plus ABS. Compared with PC, the filling pressure and melt flow rate of PC plus ABS drop significantly. The decrease in filling pressure and melt flow rate can restrain the generation of jetting. The temperature of the front melt flow reaches 259.4 ℃. There is no lack of material at the end of the product, but there are still slight smelting marks, which can be completely solved by creating discharge vents.
Figure 6 Filling analysis results of PC plus ABS
By using PC plus ABS instead of PC as the material of the parts, the jetting of the back case can be solved. Figure 7 shows the trial product, which has a smooth appearance, no defects, and meets the design requirements. The size of the trial product is tested and it meets the design requirements.
Figure 7 The trial production of the back case
5. Conclusion
The flow mark of mirror products is improved by changing the molding parameters such as pressure maintaining in this article, combined with causes and measures of flow marks and jetting. For the jetting of back covers of mobile phones, analyze the flow and filling of different plastic materials by using Moldflow. The molding material of the product was changed from the original PC to PC plus ABS. After the trial production, the appearance and size of the product met the design requirements.